Индивидуальное изготовление металлических корпусов для оборудования
- 19 марта 2019
- Служба новостей
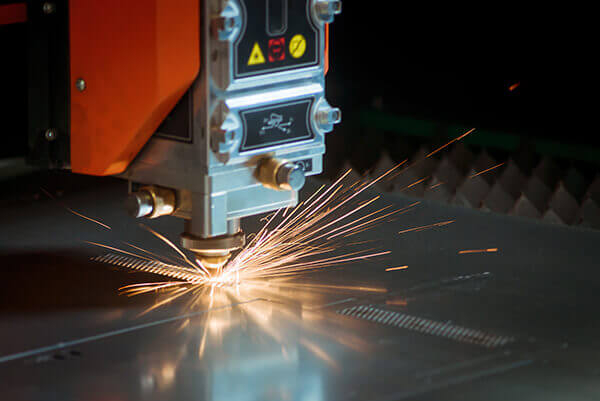
Оборудование сетевого, защитного, развлекательного, медийного, тестового, испытательного, телекоммуникационного, электротехнического, измерительного, медицинского, климатического предназначения часто используется в агрессивных условиях. Это увеличивает риск его повреждения и выхода из строя. Чтобы уберечь технику от негативного влияния от посторонних факторов, применяются корпусы из металла, производимые индивидуально.
Основные этапы изготовления продукции
Производство корпусов – комплексный состав работ. В него входят:
- проектирование изделий;
- резка на части лазерным оборудованием;
- механическая гибка;
- покрытие защитными веществами;
- создание запрессовочного крепежа и сварка;
- порошковая окраска и нанесение надписей, рисунков методом шелкографии.
Проектирование будущих корпусов
Первый этап производства предполагает создание трехмерной модели и разработку чертежей. Это выполняется на основании технического задания заказчика. При проектировании определяются размеры конструкции и ее строение, функциональные характеристики, дизайн. Полученные данные используются для предварительного расчета стоимости работ и материалов. Конструктивные документы проходят согласование и отправляются на производство, где создается первый образец.
Раскрой металла лазерным оборудованием
Резка лазером выполняется на современном высокотехнологичном оборудовании. Метод имеет много преимуществ по сравнению с другими технологиями:
- высокая скорость раскроя;
- возможность создания сложных геометрических контуров;
- минимальный объем отходов;
- точность по параметрам и отсутствие дефектов на кромках.
Способом лазерной обработки материалов выполняется изготовление корпусов из листового металла толщиной до 14 мм.
Гибка заготовок на станках
Этот механический метод воздействия базируется на пластической деформации. Изгибание позволяет сохранить монолитность изделий, снизить количество стыков и отверстий, сократить производственные расходы. Технология подходит для работы с разными по составу и типу материалами. Она выполняется несколькими способами.
Нанесение защитных покрытий
Внешний вид и эксплуатационные характеристики готовых корпусов зависят от применяемых технологий обработки металлов. Рациональным и проверенным вариантом является оцинковка. Она позволяет получать блестящие и полублестящие поверхности.
Современные покрытия, применяемые на этом этапе, отличаются надежной адгезией, экологичностью, декоративностью, надежностью. С их помощью металл приобретает защиту от коррозии и меньше подвергается загрязнениям.
Формирование запрессовочного крепежа и сварка
При необходимости соединения деталей конусообразной или цилиндрической формы используется запрессовочный крепеж. Его основные элементы – штифты, гайки, шпильки, винты и т. д. Преимущества таких деталей заключаются в прочности, отсутствии выступающих частей, стойкости перед различными нагрузками.
Сварка выбирается при скреплении заготовок разной длины. Это универсальный метод, реализуемый ручным, автоматическим способами. Если нужно получить невидимые соединения оптимальным решением является точечная технология.
Декоративная обработка, маркировка
При необходимости готовые корпусы подвергаются покраске. Процесс выполняется с применением порошковых составов. Они дополнительно оберегают металл от влаги и придают ему требуемые эстетические качества.
Маркировка, наименования, написание обозначений на поверхностях указанных наносятся методом шелкографии. Для этого используются трафареты и красящие составы разной плотности, в том числе имеющие необычные эффекты.